Need a Pallet Racking Inspection by our SEMA Approved Racking Inspectors? Trust A-Z Rack Inspections Ltd - Call 07917 664940 or 07947 886161 today!!
Pallet Racking Damage Types
Identify & Prevent Racking Damage with Expert Inspections
Maintaining safe, compliant pallet racking is essential for warehouse efficiency and employee safety. Regular inspections help prevent accidents, reduce costly repairs, and ensure compliance with HSE, PUWER, and SEMA safety regulations.
At A-Z Rack Inspections Ltd, our SEMA Approved Racking Inspectors (SARIs) conduct comprehensive racking inspections to identify damage, structural risks, and compliance issues before they escalate.
📞 Book Your Racking Inspection Today! – Call 07917 664940 or 07947 886161 📧 sales@a-zrackinspections.co.uk
Key Areas Inspected for Racking Damage
During a racking inspection, we assess:
✔ Pallet Condition & Placement – Ensuring properly positioned, undamaged pallets.
✔ Load Distribution – Checking for overloading, uneven stacking, and incorrect weight distribution.
✔ Racking Damage – Identifying impact damage from mechanical handling equipment (MHE).
✔ Floor Condition & Racking Stability – Ensuring racking is securely anchored with no floor damage.
✔ Housekeeping & Maintenance – Evaluating warehouse cleanliness, debris risks, and safe access.
✔ Modifications & Structural Changes – Checking for unauthorised racking alterations that compromise safety.
📄 Post-inspection, you’ll receive a detailed report with risk classifications (Red, Amber, Green) and recommended actions.
Pallet Racking Damage Risk Categories
Damage to racking is classified using SEMA’s Red, Amber, Green (RAG) system, which helps businesses prioritise safety actions.
🔴 Red Risk – Immediate Danger
🚨 Severe damage exceeding twice SEMA limits
🚨 Requires immediate offloading & isolation
🚨 Racking must not be used until repaired
Red Risk poses a serious hazard and must be addressed immediately to prevent collapse or injury.
🟠 Amber Risk – Requires Action Within 4 Weeks
⚠️ Exceeds SEMA limits but not critical
⚠️ Area must not be reloaded once emptied
⚠️ If not repaired in 4 weeks, it escalates to Red Risk
Amber Risk indicates moderate structural issues that must be addressed before further use.
🟢 Green Risk – Monitor & Record
✅ Minor damage within SEMA safety limits
✅ Requires monitoring during future inspections
✅ Can worsen over time, requiring reclassification
Green Risk does not require immediate action, but continued monitoring is essential to prevent deterioration.
Why Regular Racking Inspections Are Essential
✔ Ensure HSE, PUWER & SEMA Compliance – Annual expert inspections are legally required.
✔ Prevent Accidents & Collapses – Detect damage early to avoid workplace injuries.
✔ Reduce Repair Costs & Downtime – Proactive maintenance prevents costly emergency repairs.
✔ Improve Warehouse Efficiency – Safe racking ensures uninterrupted operations.
💡 Under HSE’s HSG76, businesses must conduct racking inspections at least once every 12 months by a SEMA Approved Racking Inspector.
📞 Ensure compliance today – Call 07917 664940 or 07947 886161.
Request a Racking Inspection Quote:
Typical Racking Damage Types:
Damaged Upright
Damaged Frame Bracing
Damaged Rackend Protector
Twisted Baseplate
Dislodged Beam
Damaged Beam
Corroded Baseplate
Unsafe Pallet Loads
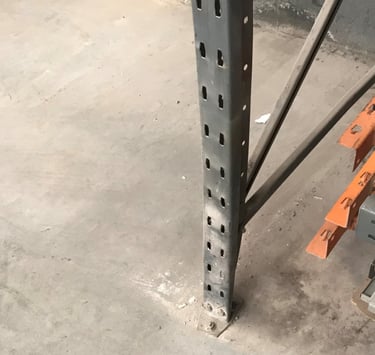
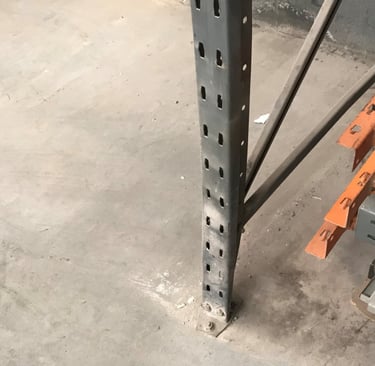
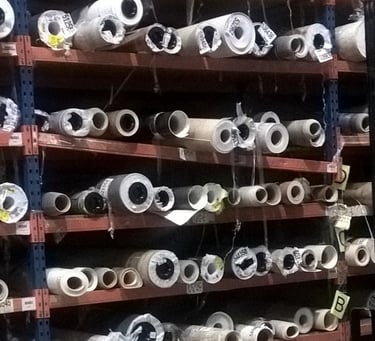
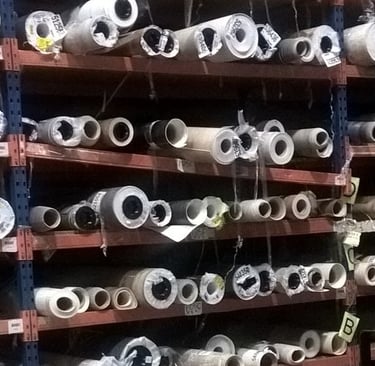
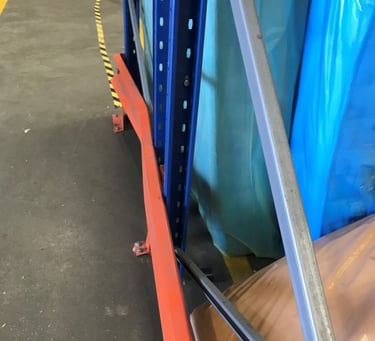
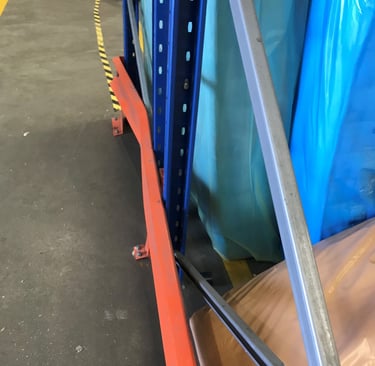
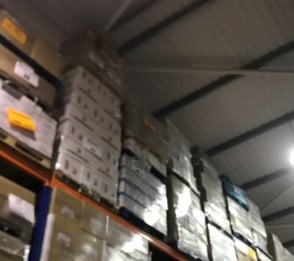
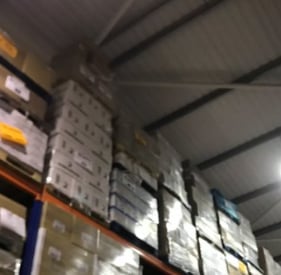
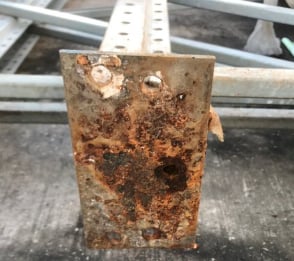
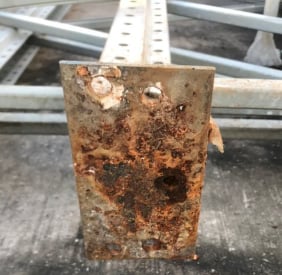
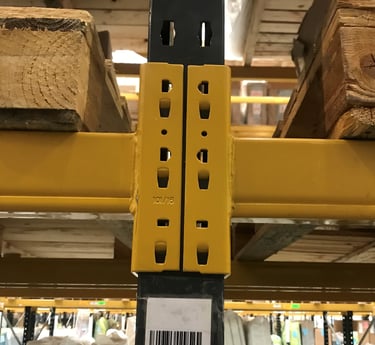
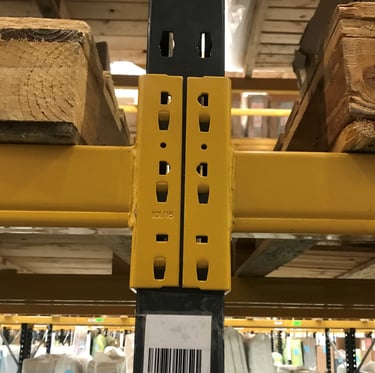
Missing Beam Locks
Damaged Floor Fixing
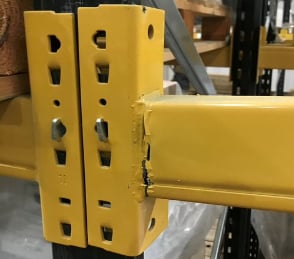
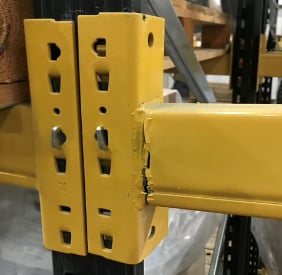
Cracked Beam Connector
Dislodged Levelling Shims
Get a Quote
With over 25 years of experience, our SEMA Approved Racking Inspectors offer nationwide Racking Inspection and Racking Safety Training.