Top 5 Common Racking Hazards and How Training Can Help Prevent Them
Need a Annual Racking Inspection by our SEMA Approved Racking Inspectors? Trust A-Z Rack Inspections Ltd - Call 07917 664940 or 07947 886161 today!!
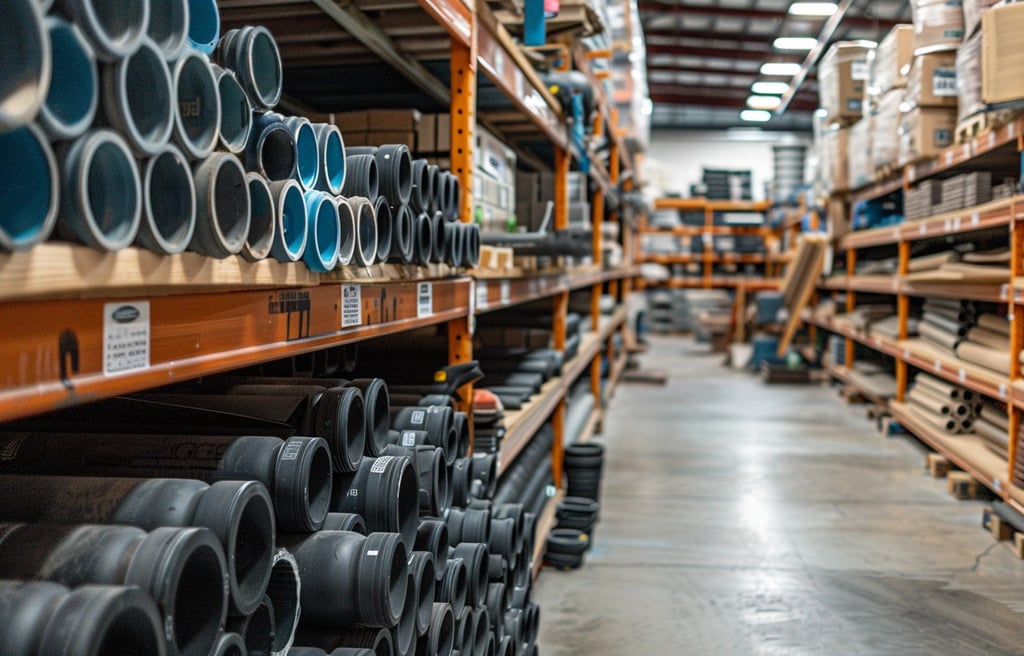
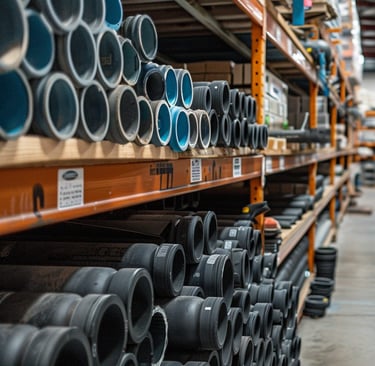
Top 5 Common Racking Hazards and How Training Can Help Prevent Them
In the fast-paced world of warehouse storage, pallet racking systems are essential for maximizing space and ensuring efficient inventory management. However, racking safety is often overlooked, leading to potential risks such as rack collapses, workplace injuries, and inventory damage. By recognizing these hazards and investing in racking safety training, warehouse operators can significantly improve warehouse compliance and health and safety standards.
This blog explores the top five most common racking hazards and how structured racking safety training can mitigate these risks, ensuring a safe warehouse environment.
1. Overloaded Racking
The Hazard:
Overloaded racking is a major cause of warehouse accidents. Every pallet racking system has a specific load capacity, and exceeding this can cause beams to bend or collapse, leading to serious injuries and damage to goods.
Prevention through Training:
Proper racking training programs educate warehouse staff on load distribution, weight limits, and capacity signage. Employees must be trained to identify racking load ratings and ensure proper placement of goods to prevent excessive stress on racking components. SEMA Approved Racking Inspectors (SARI) emphasize the importance of compliance with racking weight limits to maintain workplace safety.
2. Improper Stacking Techniques
The Hazard:
Improper stacking methods, such as uneven weight distribution or stacking products too high, can create instability, increasing the risk of items falling and causing injuries.
Prevention through Training:
A structured warehouse safety training program teaches employees how to stack items securely, ensuring proper use of palletized loads and racking configurations. Training helps staff understand the HSE guidelines on pallet stacking safety and how to prevent racking collapses caused by incorrect loading techniques.
3. Racking Damage from Equipment Impact
The Hazard:
Forklift collisions with racking systems are one of the leading causes of rack damage. Even minor impacts can weaken the structure, leading to compromised load capacity and potential collapses.
Prevention through Training:
Comprehensive forklift safety training ensures that operators understand proper maneuvering techniques around racking systems. Racking inspection training also teaches employees how to spot damage early and report it before it leads to structural failure. Businesses should enforce strict rack protection measures, such as end guards and upright protectors, to minimize damage.
4. Lack of Regular Racking Inspections
The Hazard:
Without regular racking inspections, minor structural weaknesses can go unnoticed, leading to severe accidents. Bent uprights, missing safety pins, or rusted beams can compromise racking integrity.
Prevention through Training:
HSE warehouse racking guidelines recommend weekly internal racking checks conducted by trained warehouse staff and annual racking inspections by SEMA Approved Inspectors. Employees should be trained to conduct visual inspections, identify damage indicators, and report concerns promptly. Following the HSG76 Warehouse and Storage Safety Guide ensures compliance with UK racking safety regulations.
5. Failure to Use Personal Protective Equipment (PPE)
The Hazard:
Not using PPE in warehouses increases the risk of serious injuries. Employees working near tall racking systems or handling heavy loads must wear helmets, gloves, and steel-toe boots to prevent injuries from falling objects.
Prevention through Training:
A dedicated warehouse safety program should emphasize the importance of PPE compliance. Employees should be trained on how to correctly wear and maintain PPE, as well as the legal requirements for protective gear in storage facilities.
Conclusion: Why Racking Safety Training is Essential
Understanding and mitigating racking hazards is essential for warehouse safety compliance. Addressing these top five common hazards—overloading racks, improper stacking, equipment damage, lack of inspections, and PPE negligence—reduces risks and enhances workplace efficiency.
Racking safety training plays a crucial role in ensuring warehouse workers have the knowledge and skills to prevent accidents. Racking Inspections and regular health and safety training sessions create a culture of safety, compliance, and efficiency.
If you’re looking to enhance your warehouse safety program, contact A-Z Rack Inspections today for expert racking inspection services and tailored racking safety training solutions.
📞 Call us: 07947 886161 or 07917 664940
📧 Email us: sales@a-zrackinspections.co.uk
Request a Racking Inspection Quote
Get a Quote
With over 25 years of experience, our SEMA Approved Racking Inspectors offer nationwide racking inspection and training.